prides itself as a plating solution provider for ALL types of super engineering plastics. Our mission lies in
“plating on un-plateable materials”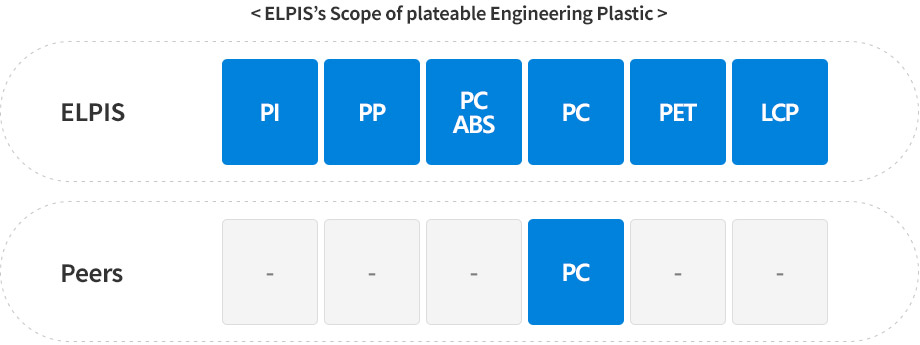
Polycarbonate is a durable material. Although it has high impact-resistance, it has low scratch-resistance. Therefore, a hard coating is applied to polycarbonate eyewear lenses and polycarbonate exterior automotive components. It is mainly used for electronic applications that capitalize on its collective safety features. Being a good electrical insulator and having heat-resistant and flame-retardant properties, it is used in various products associated with electrical and telecommunications hardware. It can also serve as a dielectric in high-stability capacitors. In the automotive industry, injection-molded polycarbonate can produce very smooth surfaces that make it well-suited for sputter deposition or evaporation deposition of aluminium without the need for a base-coat. Decorative bezels and optical reflectors are commonly made of polycarbonate. Its low weight and high impact resistance have made polycarbonate the dominant material for automotive headlamp lenses. The use of polycarbonate in automotive applications is limited to low stress applications. Stress from fasteners, plastic welding and molding render polycarbonate susceptible to stress corrosion cracking when it comes in contact with certain accelerants such as salt water and plastisol.
-
low weight
-
transparency(suited for eyewear)
-
high impact resistance
-
moderate chemical resistance
-
easy to process
-
high dimensional stability
-
heat resistance
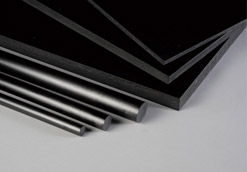
Polyamides(PA) are commonly used in textiles, automotive industry, carpets, kitchen utensils and sportswear due to their high durability and strength. The transportation manufacturing industry is the major consumer, accounting for 35% of polyamide (PA) consumption. Nylon 66 is frequently used when high mechanical strength, rigidity, good stability under heat and/or chemical resistance are required. Nylon 66, especially glass fiber reinforced grades, can be effectively fire retarded with halogen-free products. Phosphorus-based flame retardant systems are used in these fire-safe polymers and are based on aluminium diethyl phosphinate and synergists. They are designed to meet UL 94 flammability tests as well as Glow Wire Ignition Tests (GWIT), Glow Wire Flammability Test (GWFI) and Comparative Tracking Index (CTI). Its main applications are in the electrical and electronics (E&E) industry.
-
abrasion resistance
-
thermostability
-
high hardness and stiffness
-
high damping
-
good sliding
-
chemical resistance
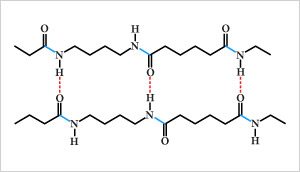
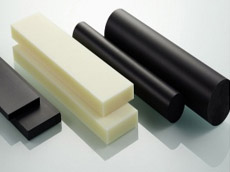