prides itself as a plating solution provider for ALL types of super engineering plastics. Our mission lies in
“plating on un-plateable materials”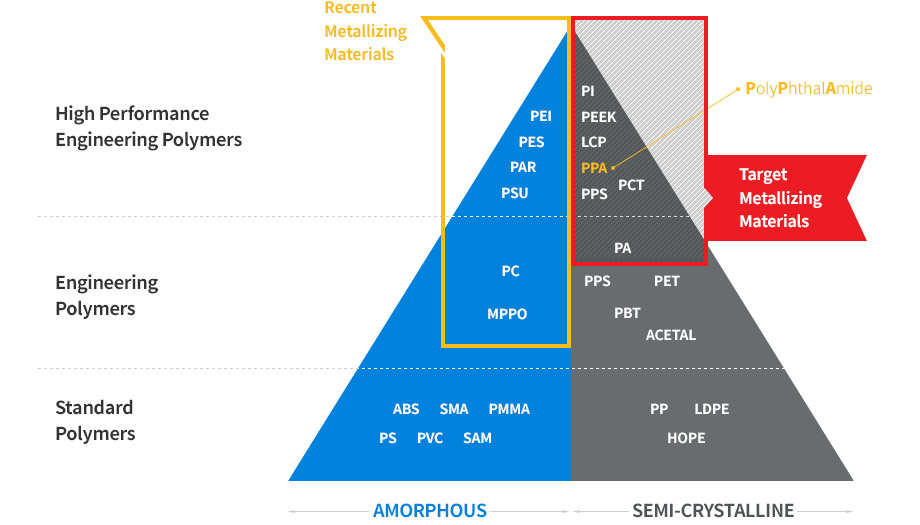
Polyphenylene sulfide is an engineering plastic, commonly used today as a high-performance thermoplastic. PPS can be molded, extruded, or machined to tight tolerances. In its pure solid form, it may be opaque white to light tan in color. Maximum service temperature is 218°C (424°F). PPS has not been found to dissolve in any solvent at temperatures below approximately 200°C (392°F). An easy way to identify the compound is by the metallic sound it makes when struck.
-
high purity
-
high crystallinity
-
high insulation
-
high mechanical stiffness
-
high heat resistance
-
high chemical resistance
-
creep resistance
-
high dimensional stability against a wide range of heat and humidity
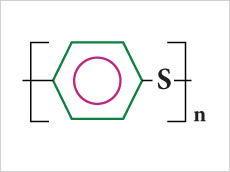
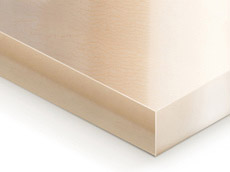
PEEK is a semicrystalline thermoplastic with excellent mechanical and chemical resistance properties that are retained to high temperatures. The processing conditions used to mould PEEK can influence the crystallinity and hence the mechanical properties. PEEK has a glass transition temperature of around 143°C (289°F) and melts around 343°C (662°F). Some grades have a useful operating temperature of up to 250°C (482°F). The thermal conductivity increases nearly linearly with temperature between room temperature and solidus temperature. It is highly resistant to thermal degradation, as well as to attack by both organic and aqueous environments.
-
high heat resistance
-
high chemical resistance
-
high radiation resistance
-
abrasion resistance
-
low smoke and toxic gas emission
-
hydrolysis resistance
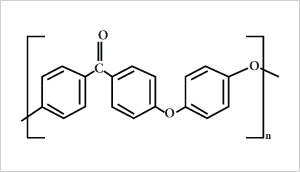
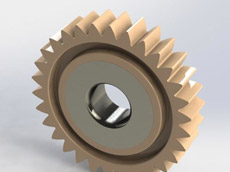
Thermosetting polyimides are known for thermal stability, good chemical resistance, excellent mechanical properties, and characteristic orange/yellow color. Thermoset polymer matrix polyimides exhibit very low creep and high tensile strength. These properties are maintained during continuous use to temperatures of up to 232°C (450°F) and for short excursions, as high as 704°C (1,299°F).[11] Molded polyimide parts and laminates have very good heat resistance. Normal operating temperatures for such parts and laminates range from cryogenic to those exceeding 260°C (500°F). Polyimides are also inherently resistant to flame combustion and do not usually need to be mixed with flame retardants. Typical polyimide parts are not affected by commonly used solvents and oils – including hydrocarbons, esters, ethers, alcohols and freons. They also resist weak acids but are not recommended for use in environments that contain alkalis or inorganic acids. The solubility properties lend them towards spray and low temperature cure applications.
-
insoluble
-
thermal stability(for long term 300℃, short term 400℃)
-
high heat resistance(up to 470℃)
-
cryogenic up to (-) 270℃
-
strong hardness and stiffness at over 260℃
-
high thermal and electrical insulation
-
emission of pure and low gas in a vacuum
-
high processability
-
flame retardant
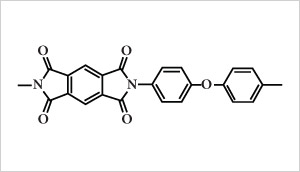
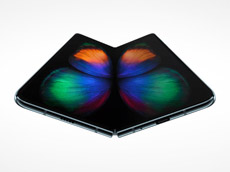